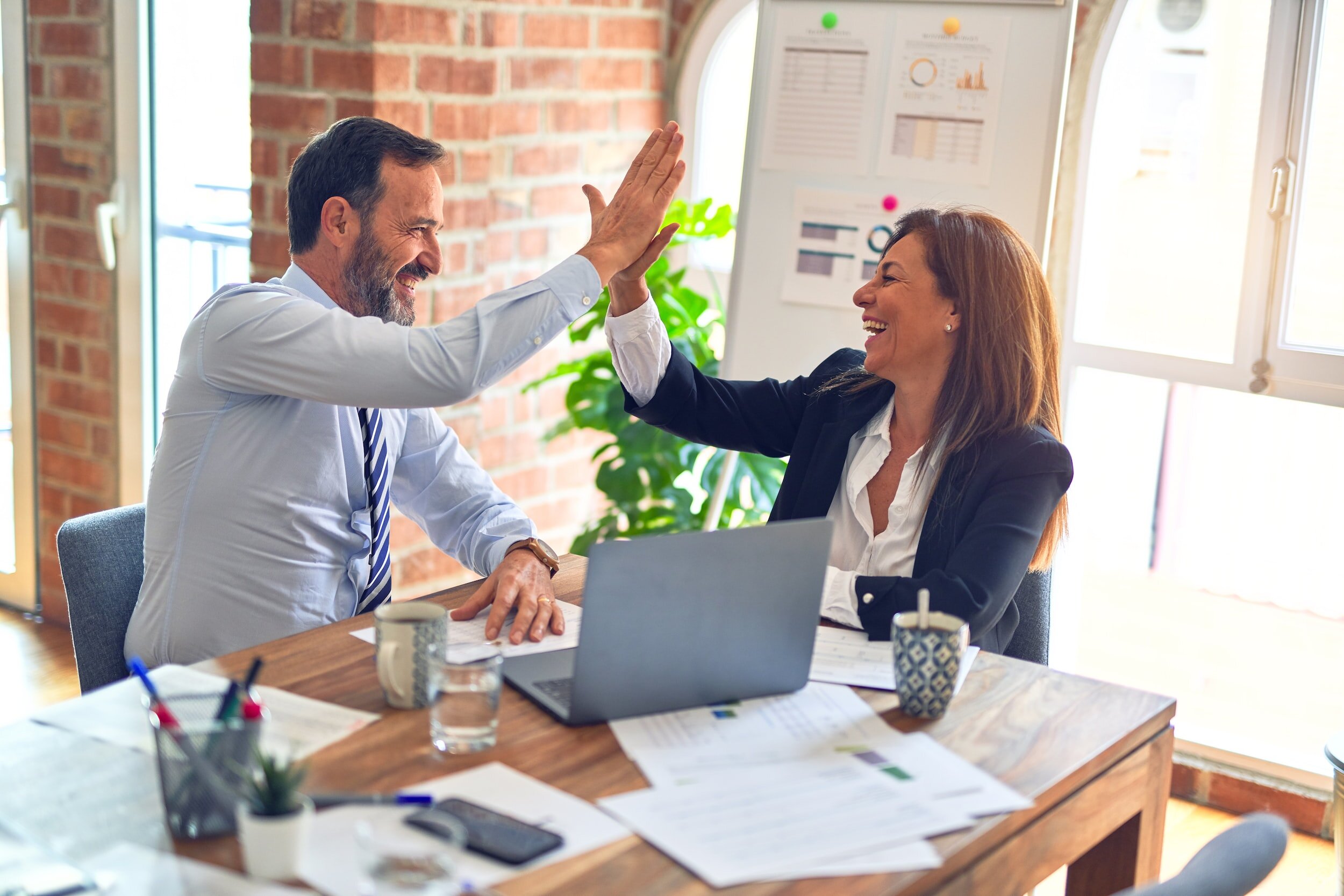
Maximizing Business Performance
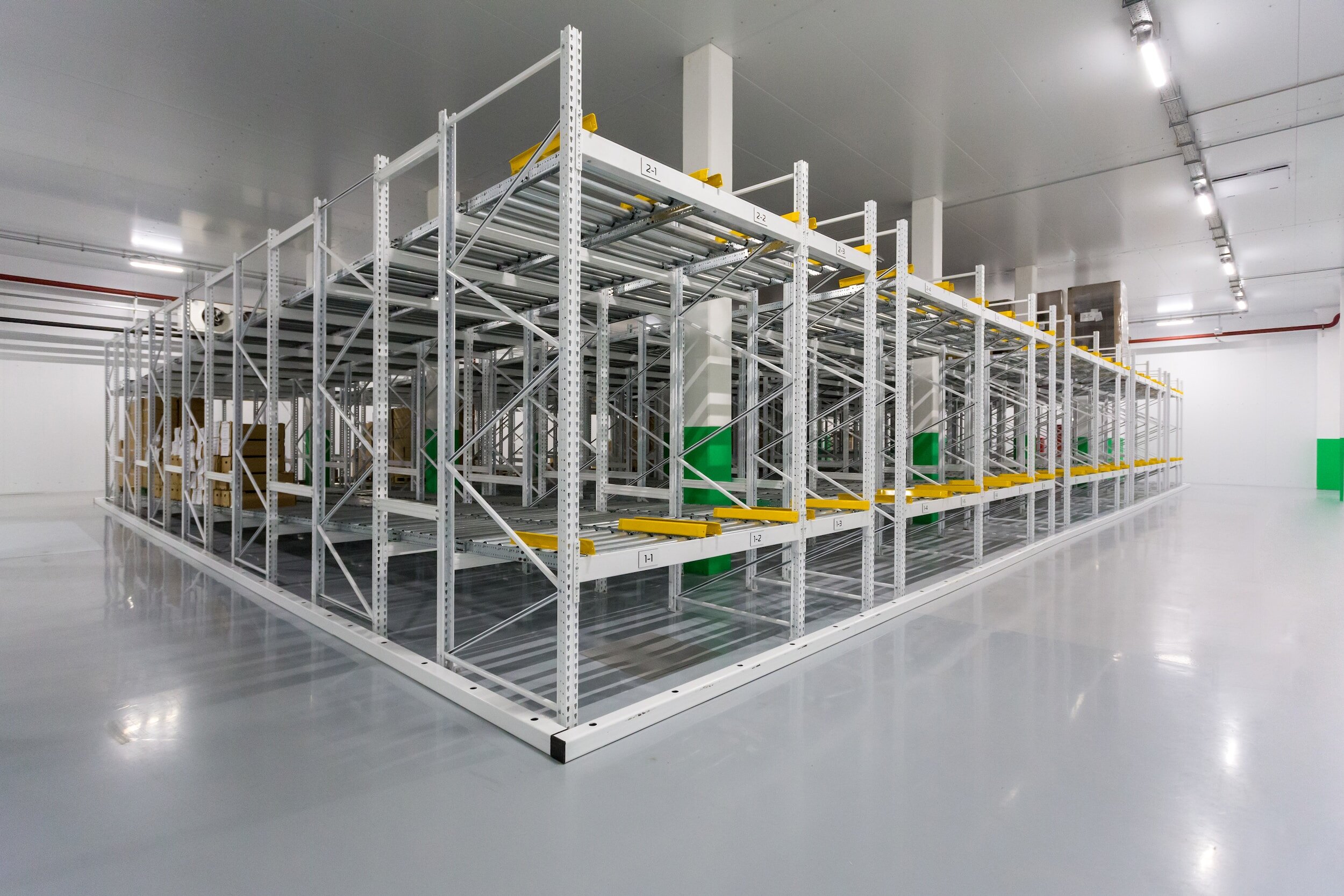
Case Studies
Private Enterprise - National Aluminum Fabrication and distribution
This National Company has over 400 employees and was experiencing gaps in performance across multiple locations. They had grown at an accelerated rate and the current process was not keeping pace with increased demand. Resulting in variances in outcomes affecting the bottom line.
K|M Team Identified opportunities to close the performance gaps and Increase Operational efficiencies through;
Comprehensive data analysis, validate performance against benchmark operational efficiencies
Map Operational Workflow to identify the system of communication and accountability
Use Performance Improvement Tools to increase accuracy and relevance in existing systems.
Incorporate Internal Auditing procedures for greater compliance.
Achieved greater cohesion across multiple locations, defined metrics including, KPIs, process stages and “gateways” for measuring progress and handover procedure at each level of the organization resulting in an increased level of accountability and consistency in organizational performance.
18% Cost Reduction in Processing in the First Month of Implementation. 28% Increase in Process Compliance.
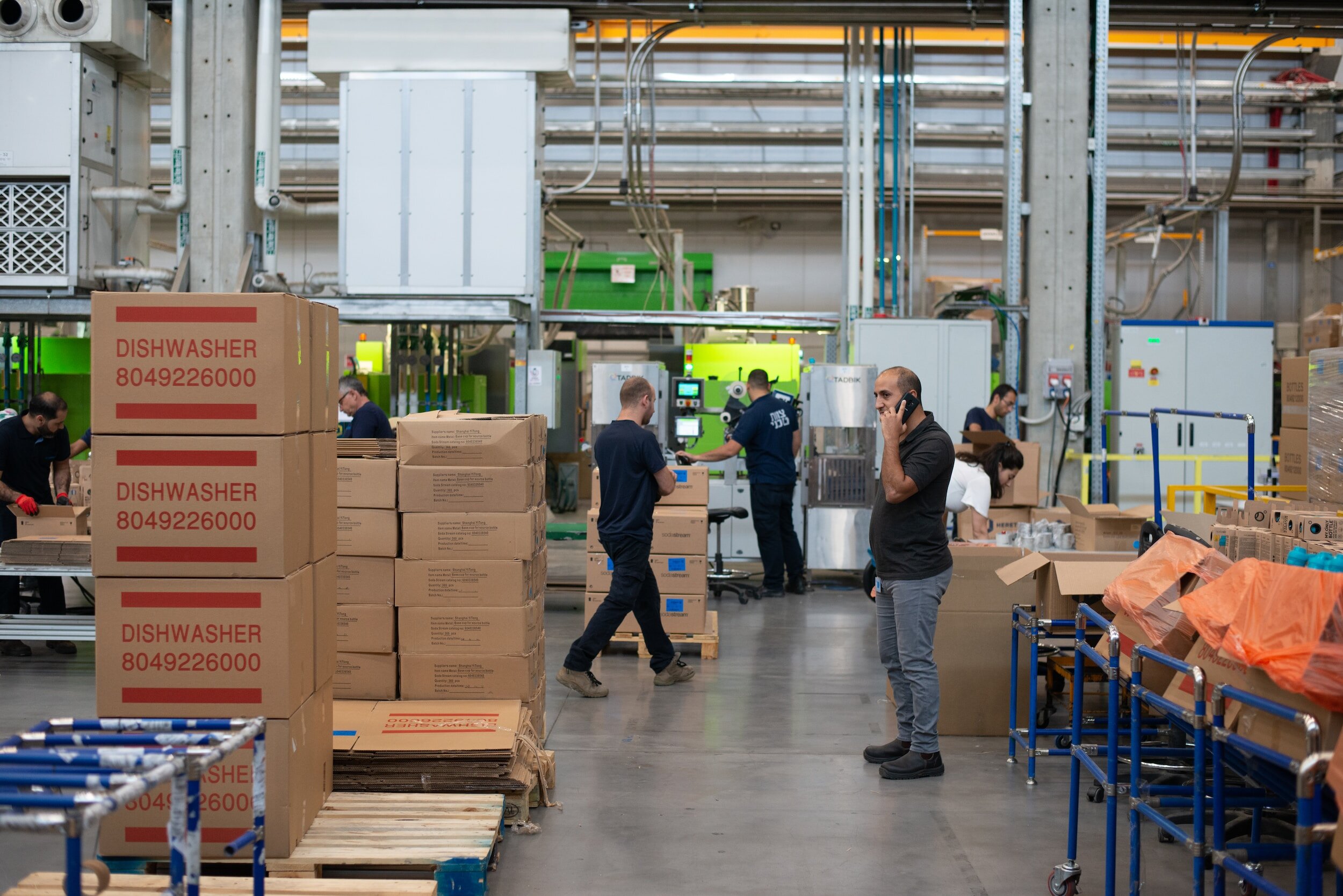
Case Studies
Project Profile
This Manufacturing Company was experiencing challenges in achieving progress to specific timelines. Supply Chain Interruptions and Increasing Operating Costs were identified as key “pain points”
K|M Inc. were challenged to identify opportunities to maximize efficiencies to assist with reduction of operating costs and Incorporate Process adjustments to better Utilize Resources and mitigate schedule slippage.
Through our unique Phased System we uncovered focused Performance Improvement measures to accomplish the clients goals. After Collaboration and Input from our Client we proceeded with Implementation, yielding desired results.
Project Highlights
Mapping existing workflow using Root Cause and G.A.P Analysis we targeted areas for Improvement that provide the greatest Impact for cost reductions and schedule gain.
Coached Site Leaders - focused on areas for Optimizing Efficiencies and better planning to minimize scheduling risk and potential bottlenecks to progress.
Coached key People to Become Continuous Improvement Champions driving engagement and ensuring sustainability.
Manufacturer experienced a significant reduction in operating costs resulting from Embedding Optimization of Process Improvements and reduced Schedule Slippage by 43% in the first 3 months.
What our clients are saying
“The KM Team lived up to their commitments, they knew how to get people involved and moving in the right direction.” Director of Operations; Fintech Industries
“Supervisors who participated in the ICP Program for Manufacturers were more Productive and were eager to help their crews work smarter.” GM ; Shoreline Manufacturing
“ KM coaching team were professional and engaging for seamless integration of technology enhancements. ”
VP Manufacturing; Salt Bx Packaging Ltd.